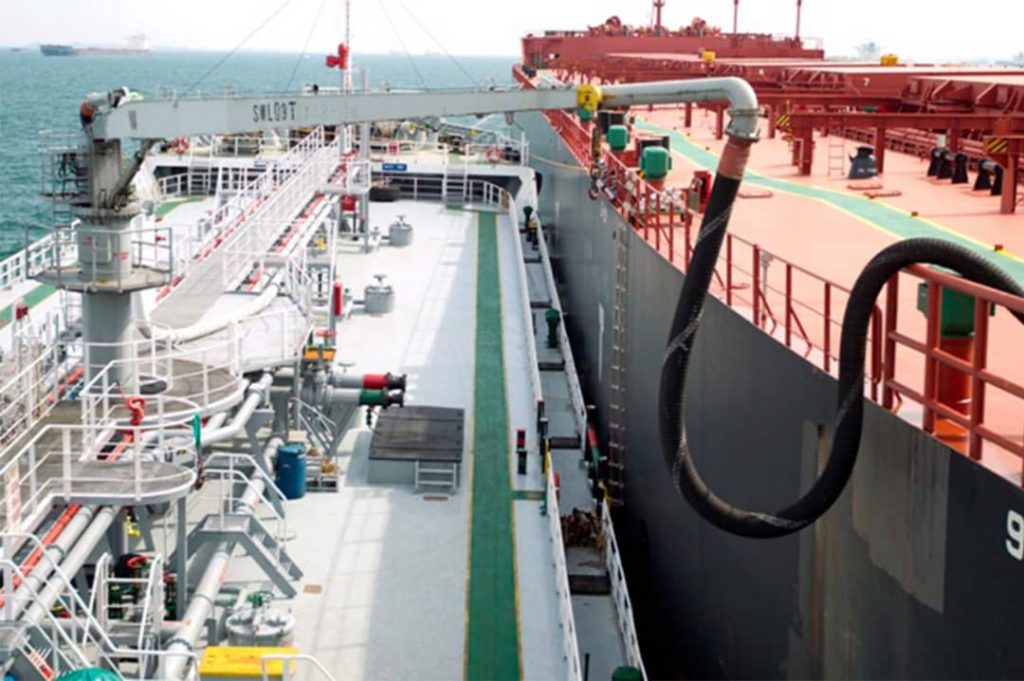
Bunkering is the supplying of fuel for use by ships, and includes the shipboard logistics of loading fuel and distributing it among available bunker tanks.
The term originated in the days of steamships, when the fuel, coal, was stored in bunkers. Nowadays the term bunker is generally applied to the storage of petroleum products in tanks, and the practice and business of refueling ships.
Bunkering operations are located at seaports, and they include the storage of “bunker” (ship) fuels and the provision of the fuel to vessels.
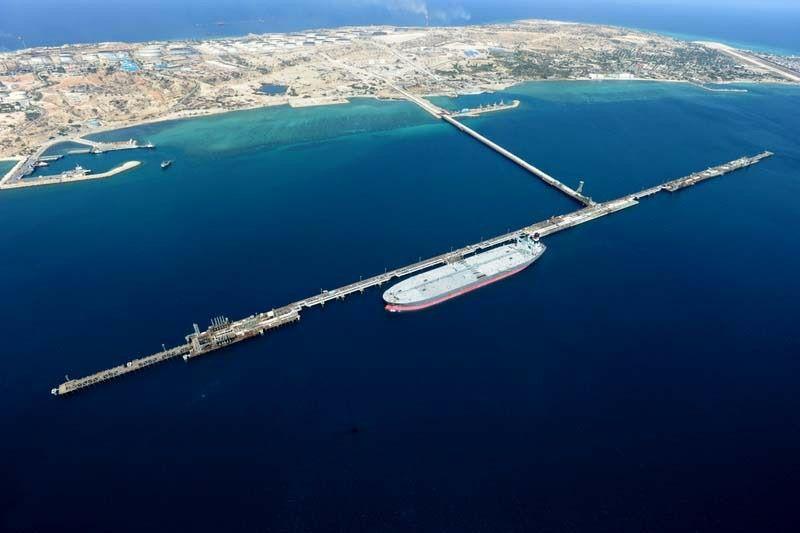
✅ Bunkering in maritime:
In many maritime contracts, such as charterparties, contracts for carriage of goods by sea, and marine insurance policies, the shipowner or ship operator is required to ensure that the ship is “seaworthy”.
Seaworthiness requires not only that the ship be sound and properly crewed, but also that it be fully fuelled (or “bunkered”) at the start of the voyage. If the ship operator wishes to bunker en route, this must be provided for in a written agreement, or the interruption of the voyage may be deemed to be deviation (a serious breach of contract). If the vessel runs out of fuel in mid-ocean, this is also serious breach, allowing the insurer to cancel a policy, and allowing a consignee to make a cargo claim. It may also give rise to a salvage situation.
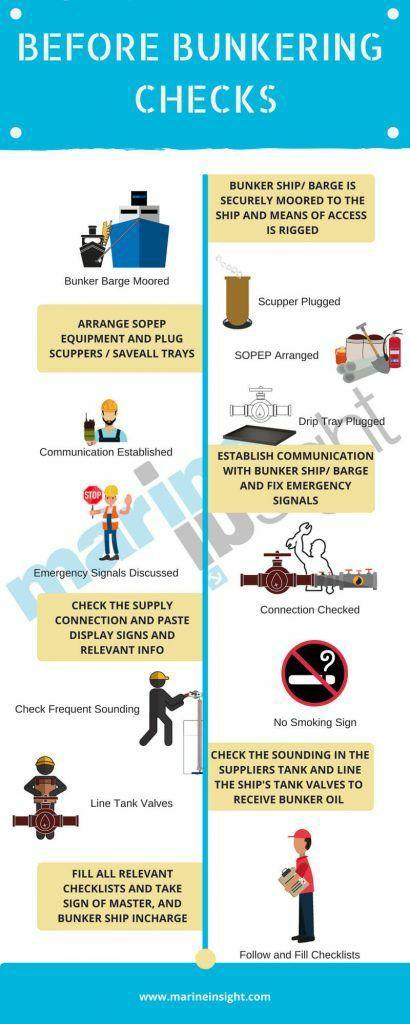
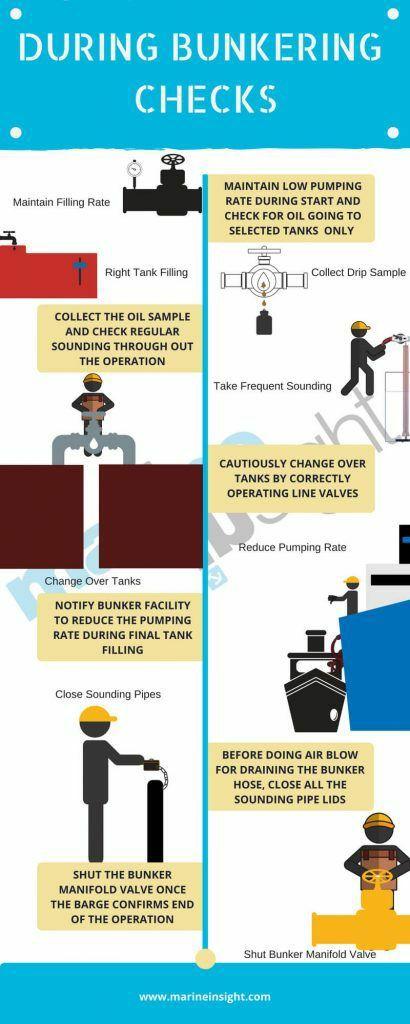
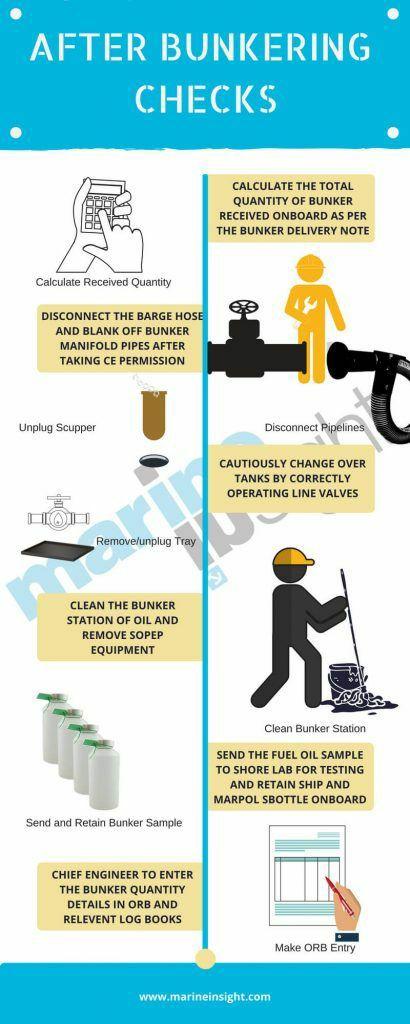
How we WORK Safety:
Safety is the foundation at GLOBAL VILLAGE BUSINESS (GVB) for all work required, both inside as well as outside the terminal boundaries.
All staff are trained extensively on relevant safety topics in the tank storage business, to ensure good safety awareness, competency and skills. Monthly mock drills and safety meetings are conducted to test and evaluate our performance. Safety at GVB is anchored in solid procedures and detailed work instructions, Permit to Work system, Management of Change, Lock out-tag out and Confined Space.
Operations:
Operations at GVB will only be planned/carried out once a written work order is issued to operations via the Terminal Automation System (TAS) called Qino. The Central Control Room (CCR) is manned 24/7 by experienced professional staff to monitor all ongoing operations, and to use the SCADA system to operate the highly automated GVB terminal. Tank levels, temperatures, flowrates, line pressures are continuously monitored physically and through instrumentation like autonomous high level alarms, unauthorized movement alarms and pressure sensors.
Innovations:
Ensuring work is carried out safely and efficiently, GVB utilizes several innovative solutions. Our fully integrated Qino TAS system caters for the complete Order to Cash process and is also connecting most departments to this unique platform. By digitalizing all these processes GVB is capable to create a consistent work environment with high reliability, transparency, and traceability. Capptions is our terminal inspection software, which helps GVB to maintain a high level of control at the terminal. A digital smartboard is used for shift handover, and is updated constantly from CCR to provide “real time” insight in operations to all staff.
Operational Excellence:
By combining the highest safety standards, innovative solutions and everyone at GVB working together as a team of highly skilled and professional employees, we are able to keep our focus on providing the most excellent operations and service to our valued customers.
At GVB we operate safely and do it “first time right”!